By Hydrogen Council
In a groundbreaking collaboration, Daimler Truck and Linde have developed a revolutionary refueling technology for subcooled liquid hydrogen, sLH2, that promises to transform long-haul trucking. Here, Roland Dold, Head of Advanced Engineering, Mercedes-Benz Trucks, and Markus Bachmeier, Director Markets & Customer Development, Linde Hydrogen FuelTech, sit down with the Hydrogen Council to explore how sLH2 technology could make hydrogen-powered trucks a cost-effective and efficient reality, potentially reshaping the future of sustainable transportation across Europe and beyond.
Markus, Roland, thank you for taking the time answering our questions. Both Linde and Daimler Truck jointly developed sLH2, an innovative refueling technology for subcooled liquid hydrogen. Most recently, the first public sLH2 fuel station was inaugurated in Wörth am Rhein, Germany. What is needed from your perspective in terms of infrastructure to successfully establish hydrogen and hydrogen-powered vehicles in Germany and Europe?
Roland Dold: Daimler Truck has committed itself to the Paris Climate Agreement. The objective is to offer only new vehicles that are CO2-neutral in driving operation in our global core markets – Europe, USA, Japan – by 2039. Truly local CO2-neutral transportation only works with zero-emission drive technologies, e.g. battery-electric and hydrogen-based. The energy can come from two sources: from batteries or by converting hydrogen into electricity on board the vehicle. When it comes to hydrogen, Daimler Truck and Linde have developed a liquid hydrogen refueling standard which we call sLH2 and opened a first refueling station to demonstrate the technology. Although we engage in and support other infrastructure initiatives (e.g. H2 Mobility in Europe or Greenlane in the US as well as with Masdar to investigate the possibilities of supplying green liquid hydrogen), Daimler Truck focusses on the development of hydrogen powered trucks such as our Mercedes-Benz GenH2 Truck. We are now calling on energy and infrastructure companies to follow our approach and build up the necessary sLH2 infrastructure.
Markus Bachmeier: The growing interest in this hydrogen technology from both hydrogen station operators and traditional fuel retailers is due to various advantages: trucks with the newly developed sLH2 onboard storage tanks can travel distances over 1,000 km (620 miles) and refuel at the same speed as today’s diesel trucks. To bring this technology “on the road” one must ensure the economically viable use of trucks and a reliable demand of fuel (hydrogen). Therefore, the first hydrogen refueling stations need to be placed strategically along the main truck routes. This will eventually lead to a reduction of refueling costs and the network can then be expanded to cover the main traffic corridors on a regional, national, and European level.
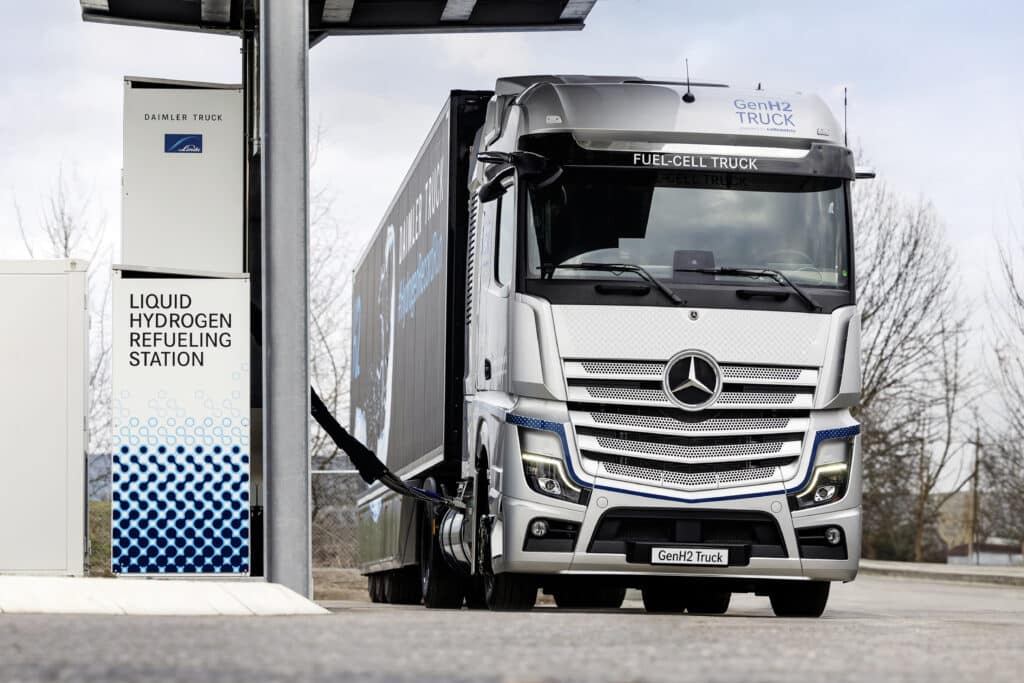
One of your goals was to make sLH2 technology openly available through ISO standard. What was the rationale behind this decision and how is it progressing?
Markus Bachmeier: Daimler and Linde have decided early on that enabling the standardization of this technology would be an important target. During the joint development process, our companies have established standards that other players can now adopt, so that they don’t have to start from scratch. This standardization is vital for the broader industry as it provides for easier integration and enables further innovation. There is, for example an emerging consensus among multiple providers to align on a standardized geometry for coupling systems (nozzles and receptacles) and refueling protocols. This will significantly broaden the choice of subcomponents and suppliers, ensuring that all stations can utilize the same coupling configurations. These standards are meant to ensure that every truck can be refueled at every hydrogen refueling station, independently of the supplier.
Roland Dold: With our Mercedes-Benz GenH2 Truck, we are aiming for flexible and demanding long-haul applications with similar performance parameters as today’s diesel technology. The trucks have a gross combined weight of 40 tons and carry 80 kg of liquid hydrogen and we are able to fill those 80 kg within 10-15 minutes. We prefer liquid hydrogen, as the energy carrier in this aggregate state has a significantly higher energy density in relation to volume than gaseous hydrogen. This allows for 1000 kilometers of range and more because it is very efficient. Just last September, we demonstrated that hydrogen-powered long-haul transportation works in real life with our #HydrogenRecordRun, where one of our Mercedes-Benz GenH2 Trucks completed 1,047 km on a single filling of liquid hydrogen. The aim is that by showcasing how efficiently the refueling process works – that means safe, fast and simple – it will become widely available as the dominant hydrogen refueling technology, in turn enabling the deployment of hydrogen trucks at large scale across the planet. So we opened up a door, offering a gateway for other OEMs, infrastructure companies and associations to apply the new liquid hydrogen standard and thereby establish a global mass market for the process.
In your communication, you highlighted significant reductions in capital and operational costs for sLH2 refueling stations compared to other hydrogen stations. How will this impact the competitiveness of hydrogen-powered trucks compared to Diesel?
Markus Bachmeier: Road transport is a very cost sensitive business, so bringing down refueling station costs was a key development target for us. Linde’s sLH2 stations require significantly lower investment costs compared to alternative hydrogen refueling stations and offer a remarkably low total cost of ownership (TCO). The main drivers for that TCO reduction are high throughput as well as reduced electricity costs for operation and minimal land requirements, as well as no hydrogen losses at the station. This is especially cost-effective in areas where the land is particularly expensive which is the case for most public and private truck fueling stations in Europe. The sLH2 technology also allows for longer service intervals, which keeps station availability high and service costs low. We already see this happening at the Wörth sLH2 refueling station where the operation has been running smoothly and flawlessly since the start of operation earlier this year.
Furthermore, sLH2 technology stands out for its scalability. Compared to other hydrogen stations, the scalability comes with relatively lower cost increases. In other words: to boost capacity, sLH2 filling stations require comparatively less energy and the footprint will stay more or less the same. Another advantage of the sLH2 technology is the flexibility the station operator is given: if needed, the station can include a Linde Cryopump in addition to the sLH2 pump. With such a set-up, the station can fuel not only sLH2 trucks but also trucks that use gaseous hydrogen in the vehicle tank.
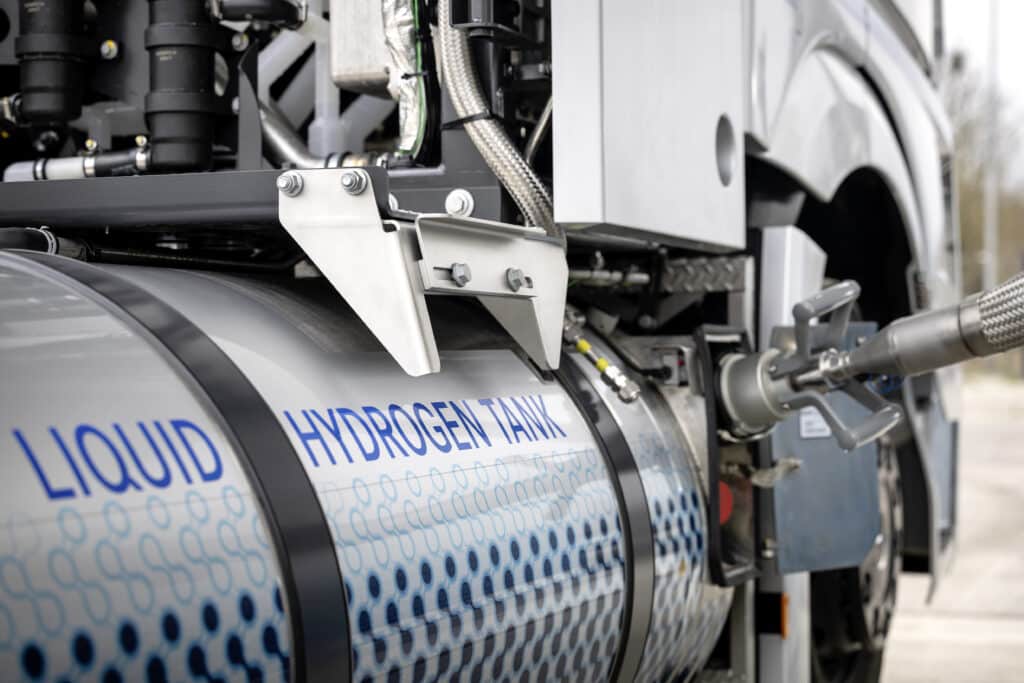
What are the advantages of taking a joint, collaborative approach like this versus each company pursuing technology development independently?
Markus Bachmaier: When it comes to hydrogen technology, we need to consider the entire value chain from the molecules to the vehicles and develop technologies hand in hand. From the start, even before the formal standardization efforts began, Linde and Daimler Truck have worked together to ensure the compatibility of the tank and the hydrogen refueling stations. This made for smooth and fast progress in the optimization of the system as a whole. In our view this approach is more efficient than optimizing each part separately and is additionally reducing R&D costs. By engineering in tandem, we avoid duplicating research and development efforts and costs, since the components are designed to complement each other from the outset.
Roland Dold: Daimler Truck intends to start customer testing of the Mercedes-Benz GenH2 Truck in Mid-2024, with the introduction of the series planned for the end of this decade. The vehicle is only one part of the equation: to make sustainable transportation possible also with hydrogen powered vehicles, we must partner across industries and look at the entire value chain of hydrogen. We at Daimler Truck are the vehicle experts and have the expertise in engineering for the development of a hydrogen powered fuel-cell truck. Linde has the same expertise on the topic of hydrogen production and distribution. So, we worked on the topic of establishing a refueling standard together, pooling important areas of competencies and gaining a time advantage to reach our goals fast. Beyond the collaboration with Linde and despite it not being our core business, we at Daimler Truck are also involved in setting up the corresponding supply chain and are making an initial push in the expansion of hydrogen refueling stations. Examples are our involvement with H2 Mobility in Europe or Greenlane in the United States. In addition to the infrastructure initiatives, we are also working with Masdar to investigate the possibilities of supplying green liquid hydrogen from Abu Dhabi (UAE) to decarbonize road freight transport in Europe.
What would be your message to other companies looking to undertake similar collaborations?
Roland Dold: Zero-emission transport needs three factors: the right battery-electric and hydrogen-powered vehicles – as we have developed with our Mercedes-Benz GenH2 Truck –, the required infrastructure network and cost parity for ZEVs compared to diesel trucks. Mastering each one of these factors involves a tremendous amount of work. Succeeding in all three of them requires collaborative effort. Therefore, we must work together, across industries and together with governments in order to have a result at the end of the equation. No one can do it alone.
Markus Bachmaier: The path to success of hydrogen heavy duty trucking, and for the development of the clean energy economy in general, will be accelerated by greater collaboration in the development and standardization of processes, as well as joint investments. It is essential for all players to not only join but to actively contribute, using the knowledge and experience gained from existing initiatives. The transport industry will benefit from aligning with the standards developed by Daimler Truck and Linde. Adopting these standards will hopefully increase the pace of vehicle and infrastructure development and roll-out. The more all players cooperate, the more successful everyone will be.
This joint development process between Daimler Truck and Linde shows that cooperation to push new technologies is a very successful way to tackle the challenges of our future.