The multi-year demonstrator program has officially been launched with the objective to test a variety of hydrogen technologies both on the ground and in the air.
The ZEROe demonstrator is a giant leap forward in Airbus’ mission to bring zero-emission aviation to reality. The designer and manufacturer of aerospace products, services and solutions to a customer base worldwide has been a steering member of the Hydrogen Council since 2018. Discover how the hydrogen combustion technology will work on the A380 test platform in the following article.
In 2015, one of the most powerful engines ever developed for an Airbus aircraft was approaching the final stages of development. But before it could be fitted to the A350-1000 aircraft for which it was destined, the engine needed to be flight and ground tested – a common practice for new technologies before entry-into-service.
That is why, on a pleasant autumn day, the aircraft equipped with the development engine took off from Airbus’ facilities in Toulouse. The test flight lasted 4 hours and 14 minutes, and analyzed the performance of a wide range of power settings at altitudes of up to 35,000 feet.
But it was not the A350-1000 used for the test flight: it was the A380 MSN1 – the first-ever A380 to roll off the production line. The A380 is the world’s largest and most spacious passenger jet ever built – a size that makes it ideally suited to the role of test platform.
Today, the A380 MSN1 test aircraft is earmarked for a new role: to take the lead on testing the technologies that will be vital to bringing the world’s first zero-emission aircraft to market by 2035.
“The A380 MSN1 is an excellent flight laboratory platform for new hydrogen technologies,” said Mathias Andriamisaina, Airbus ZEROe Demonstrator Leader. “It’s a safe and reliable platform that is highly versatile to test a wide range of zero-emission technologies. In addition, the platform can comfortably accommodate the large flight test instrumentation that will be needed to analyze the performance of the hydrogen in the hydrogen-propulsion system.”
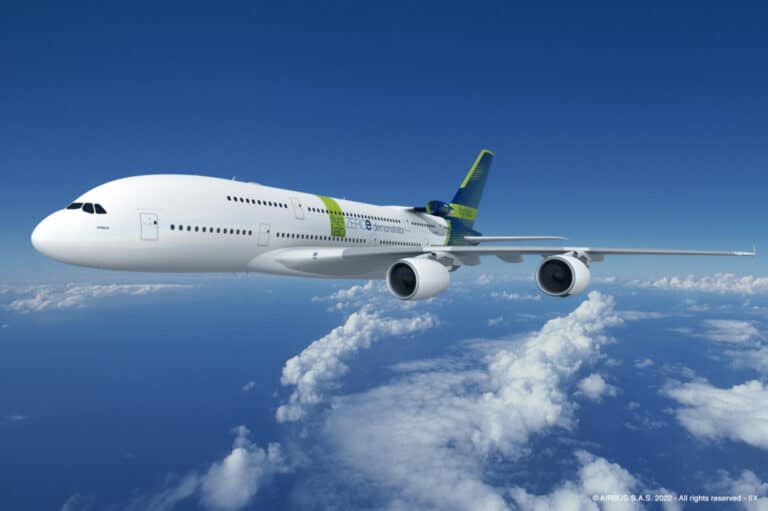
Demonstrators: testing tomorrow’s technologies today
A demonstrator aircraft is fundamental to developing new aviation technology. It is primarily used to test and prove the viability of designs, processes, fuels, materials and equipment, both on the ground and in the air. This information is then used to refine and certify the finished product. Demonstrators also serve to showcase innovation to a wider audience, from government officials and investors to journalists and the general public.
Airbus has a long track record of launching demonstrator programmes to test pioneering technology. The E-Fan family, for example, highlighted the potential for all-electric flight. The Vahana and CityAirbus demonstrators have proven invaluable in furthering Airbus’ vision for sustainable urban air mobility. And, most recently, the E-Fan X was used to test the potential of hybrid-electric propulsion.
The ZEROe demonstrator will now be the next to test groundbreaking zero-emission technologies. It will carry four liquid hydrogen tanks in a caudal position, as well as a hydrogen combustion engine mounted along the rear fuselage. The liquid hydrogen distribution system will feed into a conditioning system in which the liquid hydrogen will transform into its gaseous form before it is introduced into the engine where it is combusted for propulsion.
“This isn’t Airbus’ first experience with hydrogen-powered flight,” Mathias explained. “From 2000 to 2002, Airbus was a key partner in the European Union’s Cryoplane research project. Building on these academic inquiries, we’re proud to take the testing of hydrogen combustion to the next level.”
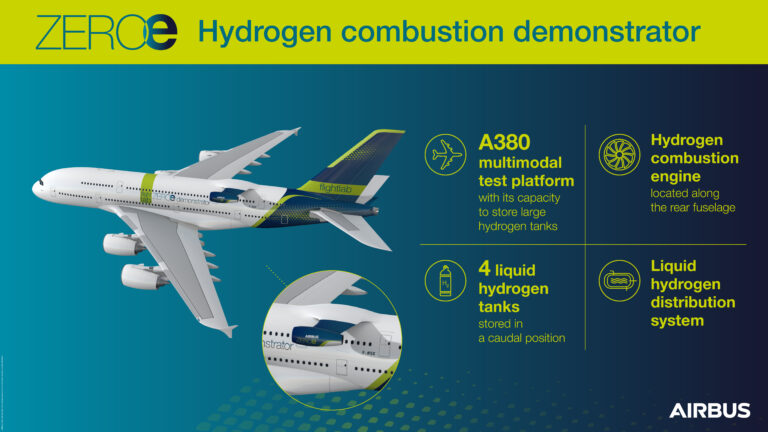
Collaborating for zero-emission aviation
The hydrogen combustion engine is a key part of the ZEROe demonstrator program. Engine manufacturers have been working hand-in-hand with Airbus on demonstrator programs for decades. And the ZEROe demonstrator will be no exception.
CFM International, a joint venture between GE and Safran, is set to develop the hydrogen combustion engine and prepare it for testing. Specifically, the company will modify the combustor, fuel system and control system of a GE PassportTM turbofan to run on hydrogen. The engine was selected due to its physical size, advanced turbo machinery, and fuel flow capability.
Each technology component – the hydrogen tanks, hydrogen combustion engine and liquid hydrogen distribution system – will be tested individually on the ground. Then, the complete system will be tested first on the ground and then subsequently in flight. The first flight is expected to take place in the next five years.